www.indo-industry.com
03
'24
Written on Modified on
Keberlanjutan dalam pemesinan: Peran apa yang dimainkan oleh pemegang tool?
Memperhatikan seluruh proses.
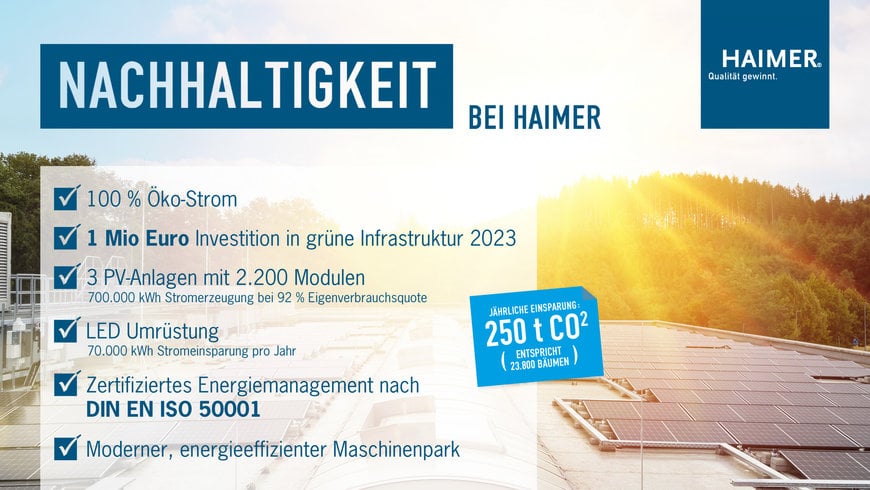
Pertimbangan keberlanjutan saat ini sedang “trendi”. Tidak terkecuali permesinan dan peralatan yang digunakan untuk itu. Elemen individual - seperti pemegang tool - sering kali dipertimbangkan. Namun, jika Anda benar-benar ingin bertindak secara berkelanjutan, Anda tidak boleh terlalu fokus pada hal-hal rinci, karena jika tidak, Anda mungkin akan kehilangan manfaat dari keseluruhan proses.
Keberlanjutan adalah topik yang kini menjadi semakin penting bagi kita. Sumber daya terbatas dan energi semakin mahal. Saat mengevaluasi keberlanjutan, penting untuk tidak berfokus terlalu sempit pada suatu produk, namun juga mempertimbangkan lingkungan – siklus hidup produk dan keseluruhan proses di mana produk tersebut terintegrasi.
Bagaimana keberlanjutan dalam permesinan?
Pemesinan logam memiliki banyak aspek. Berbagai macam mesin, perkakas, dan pemegang tool digunakan dalam proses permesinan, tergantung pada material, geometri komponen, dan kuantitasnya,. Keadaan eksternal seperti lokasi produksi, kualifikasi karyawan dan kemungkinan otomatisasi juga harus diperhitungkan. Ada banyak pilihan proses manufaktur berbeda yang dapat menjadi solusi terbaik, paling ekonomis, dan paling berkelanjutan tergantung pada kasus masing-masing. Sulit untuk tidak membandingkan apel dengan jeruk di sini.
Bagaimana keberlanjutan diukur? Selain material yang digunakan, efisiensi energi mungkin merupakan faktor utama yang menentukan proses berkelanjutan. Oleh karena itu, pendekatan yang menjanjikan adalah mencari pengguna terbesar dan mengoptimalkan penggunaannya.
Peralatan mesin menawarkan potensi penghematan
Dalam pemesinan, tidak diragukan lagi, dalam hal ini adalah mesin perkakas, yang menghabiskan sebagian besar energi adalah penggerak spindel dan sumbu, periferal, dan unit tambahan seperti pendinginan, pelumasan, atau pasokan udara bertekanan.
Saat membeli mesin baru, pengguna dapat mengurangi konsumsi secara signifikan dengan memperhatikan komponen hemat energi. Andreas Haimer, Managing Director dan Presiden HAIMER Group, pemimpin pasar dalam teknologi pemegang tool, menjelaskan: "Dalam produksi kami sendiri, kami telah belajar bahwa mengganti mesin lama dengan yang baru, dan menggunakan proses pemesinan yang sama memerlukan sekitar 30 persen lebih sedikit energi." Ia menambahkan faktor mendasar lainnya: "Sebagai bisnis keluarga, kami menaruh banyak perhatian pada keberlanjutan. Misalnya, kami menggunakan baja dari Jerman untuk peralatan, telah menggunakan listrik secara eksklusif dari sumber energi terbarukan selama bertahun-tahun, dan berinvestasi pada sistem energi surya dan infrastruktur ramah lingkungan. Pada tahun keuangan terakhir, kami menginvestasikan total lebih dari satu juta euro dan menghemat lebih dari 250 ton CO2 per tahun."
Kembali ke permesinan, dimana tidak semua mesin lama bisa diganti dengan yang baru. Penghematan juga dapat dilakukan dalam proses pemesinan, misalnya dengan menggunakan strategi pemesinan yang dioptimalkan melalui CAD/CAM seperti proses trochoidal. Andreas Haimer mempunyai contoh nyata: "Seorang pelanggan memberi data kepada kami tentang bagaimana ia mampu mengurangi waktu pemesinan sebesar 75 persen dari 71 menit menjadi 18 menit per barang dengan proses trochoidal menggunakan chuck shrink fit HAIMER Power dan alat potong HAIMER MILL kami, dibandingkan dengan pemesinan menggunakan alat potong face mill. Perubahan strategi pemesinan dibarengi dengan penghematan energi karena konsumsi daya yang jauh lebih rendah, Ketika pemesinan konvensional dengan alat potong face mill menggunakan beban spindel sebesar 80-85% untuk 10 barang, sehingga menghasilkan total biaya energi sekitar EUR 150, strategi proses trochoidal dengan beban spindel 8-10% dan waktu kerja alat yang jauh lebih singkat mengurangi biaya energi hingga total EUR 5 untuk 10 barang. Hal ini berarti output yang lebih tinggi dengan konsumsi energi yang lebih rendah per barang diproduksi - itulah yang saya sebut berkelanjutan dan efisien."
Keberlanjutan untuk pemegang tool: Pendekatan holistik
Jika Anda melihat keseluruhan rantai proses, pernahkah Anda memikirkan bagaimana pemegang tool dapat berkontribusi terhadap keberlanjutan? Mengingat proses pemesinan yang mana mesin milling mengkonsumsi rata-rata sekitar 30 kW, ditambah daya perangkat hidrolik dan pneumatik, peralatan otomasi dan robot, memegang tool hanya memainkan peran tambahan. Hal ini karena pemegang tool merupakan bagian yang relatif kecil, meskipun proses pencekaman dengan chuck shrink fit hanya memerlukan sedikit energi.
Dibandingkan sistem pencekam lainnya, konsumsi energi selama proses shrink fit lebih tinggi dalam penggunaan operasional dibandingkan dengan chuck hidrolik atau chuck milling. Tetapi, jika Anda melihat keseluruhan siklus hidup produk dari pemegang tool, yang mencakup produksi, pemeliharaan, dan pembuangan, gambaran yang sangat berbeda akan muncul.
Produksi chuck hidrolik memerlukan lebih banyak tenaga dan energi karena strukturnya yang lebih rumit. Selain pemesinan komponen individual dengan presisi tinggi, ada juga penyolderan selongsong ekspansi, perlakuan panas tambahan untuk mencegah putusnya sambungan solder, serta upaya yang diperlukan untuk pembersihan, perakitan, dan pengisian oli. “Dari pengalaman kami, energi yang dibutuhkan untuk produksi sekitar tiga kali lebih tinggi dibandingkan energi yang dibutuhkan untuk chuck shrink fit,” jelas Andreas Haimer. “Selain chuck shrink fit, kami juga memiliki chuck hidraulik dalam portofolio kami yang luas, meskipun harga jualnya dua hingga tiga kali lebih tinggi dibandingkan chuck shrink fit karena proses produksinya yang rumit. Chuck ini merupakan solusi yang tepat untuk aplikasi tertentu. Namun, bahan ini tidak lebih ramah lingkungan. Analisa kami menunjukkan bahwa chuck hidrolik memerlukan sekitar 25 kWh lebih banyak energi untuk diproduksi dibandingkan dengan chuck shrink fit. Sebaliknya, dalam hal siklus hidup produk, hal ini berarti chuck shrink fit dengan kebutuhan energi sebesar 0,026 kWh per pemanasan dan siklus pendinginan dapat digunakan hampir 1.000 kali lipat sebelum memerlukan lebih banyak energi daripada chuck hidrolik." Hal yang sama berlaku untuk chuck milling, yang jauh lebih rumit dan mengandung lebih banyak komponen serta gemuk dan pelumas.
Siklus hidup dan keandalan proses sangat penting
Selain biaya produksi yang meningkat, juga terdapat perbedaan dalam hal perawatan. Ketika chuck shrink fit Haimer bebas perawatan karena kualitas yang sangat tinggi dari baja perkakas pengerjaan panas, dikombinasi dengan koil Haimer yang dipatenkan dan teknologi mesin shrink fit, chuck shrink fit tersebut dapat dipakai dalam jumlah yang tidak terbatas, sedangkan chuck hidrolik dan chuck milling harus dikembalikan ke pabrik paling lambat setiap 2-3 tahun untuk memeriksa kekuatan pencekaman, melumasi baut penjepit atau melumasi sistem dan melakukan perawatan rutin terhadap chuck karena keausan. Cairan atau gemuk hidrolik yang terkandung di dalamnya juga membuat pembuangan yang ramah lingkungan menjadi lebih sulit dibandingkan dengan chuck shrink fit, yang tidak mengandung komponen tambahan apa pun. Selain siklus hidup, terdapat juga perbedaan signifikan dalam hal keandalan proses: jika terjadi pemesinan kering atau pendinginan yang tidak mencukupi dalam proses pemesinan, area pencekaman chuck hidraulik akan mempunyai risiko memuai dan pecah karena panas yang tinggi, termasuk alat potong terlepas dan risiko barang rusak. Chuck shrink fit lebih kuat dan tahan lama dalam hal ini; jika Anda ingin sepenuhnya menghilangkan risiko alat potong terlepas, sistem Haimer Safe-Lock tersedia sebagai opsi untuk chuck shrink fit demi keamanan 100%.
Konsumsi energi dalam perspektif
Namun bagaimana sebenarnya konsumsi energi dihitung selama proses shrinking? Memanaskan chuck shrink fit membutuhkan waktu sekitar 5 detik dengan mesin shrink fit HAIMER saat ini. Pengguna berpengalaman dapat mengeluarkan alat potong yang sudah aus dan memasang alat potong baru dalam satu pengoperasian. Oleh karena itu, chuck shrink fit hanya dipanaskan dan didinginkan satu kali. Output maksimum mesin shrink fit HAIMER Power Clamp dengan koil NG yang dipatenkan adalah 13 kW, tetapi rata-rata adalah 8 kW. Artinya, satu proses pemanasan yang menyeluruh menghabiskan sekitar 0,011 kWh. Selain itu, pendinginan menghabiskan sekitar 0,015 kWh - meskipun perangkat Haimer dapat mendinginkan hingga lima dudukan secara paralel dan pada saat yang sama dengan konsumsi energi yang hampir sama. Dalam skenario terburuk, hal ini menghasilkan total 0,026 kWh untuk keseluruhan proses. Jika satu kilowatt jam berharga 20 sen, maka penyusutan dan pendinginan alat hanya membutuhkan biaya 0,5 sen.
Dan bagaimana seharusnya konsumsi energi diklasifikasikan ketika mempertimbangkan proses permesinan, dimana konsumsi daya mesin milling dengan semua penggerak adalah sekitar 30 kW? Dengan asumsi bahwa suatu alat potong digunakan selama kira-kira 1 jam dan bahkan jika hanya satu persen waktu permesinan yang dapat dihemat berkat konsentrisitas dan kekakuan yang tinggi atau strategi permesinan yang ditingkatkan karena kontur yang ramping, maka akan menghemat energi sebesar 0,3 kWh. Ini kira-kira 11 kali lipat jumlah energi yang digunakan untuk proses shrink fit.
Andreas Haimer merangkum: "Konsumsi energi per proses pencekaman alat potong memainkan peran yang dapat diabaikan dibandingkan dengan masalah siklus hidup, keandalan proses, dan strategi pemesinan. Strategi milling CAD/CAM modern yang dioptimalkan dapat menghemat 75 persen waktu pemesinan. Para insinyur harus fokus pada perbaikan proses jika mereka ingin proses berkelanjutan dan produktif. Dan pada langkah berikutnya, mereka harus memilih pemegang tool yang paling sesuai dan dapat diandalkan dalam proses untuk strategi ini"
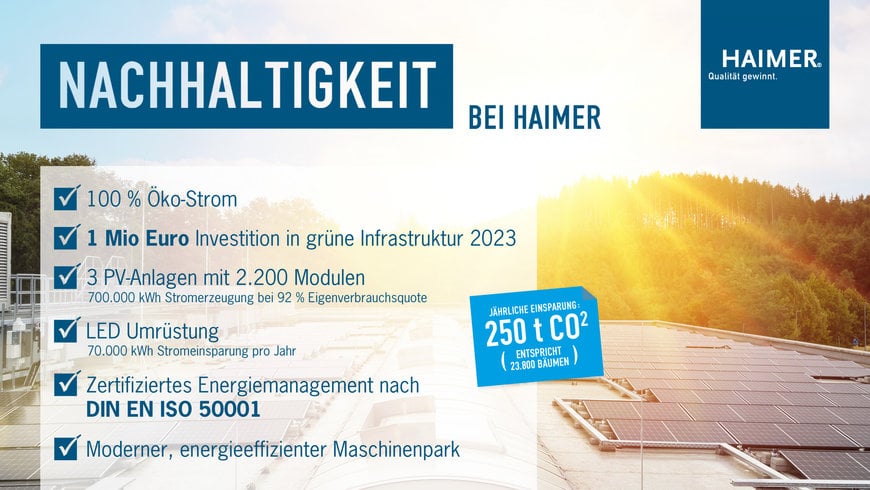
Keberlanjutan di HAIMER
Pada tahun 2023, HAIMER menginvestasikan lebih dari satu Juta Euro pada infrastruktur ramah lingkungan. Diantaranya, sistem energi surya diperluas ke bangunan lain dan diubah menjadi lampu LED. Hal ini akan menghemat lebih dari 250 ton CO2 per tahun.
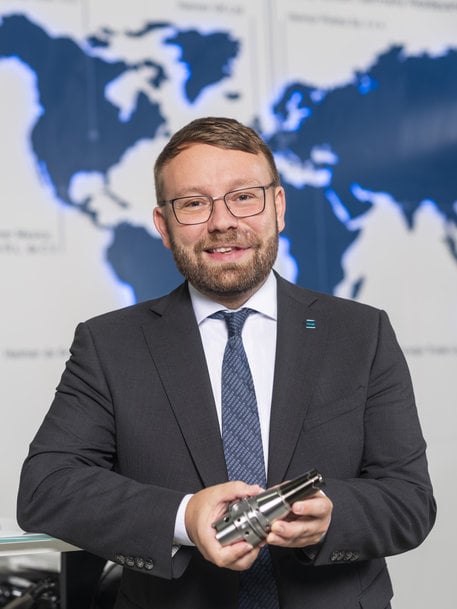
Andreas Haimer dengan chuck hibrida baru
Andreas Haimer, Presiden HAIMER Group, dengan chuck hibrida baru: "Kami memiliki berbagai macam pemegang tool yang berbeda-beda. Ini mencakup banyak model chuck shrink fit yang berbeda, dan juga chuck hidrolik. Di EMO, kami mempersembahkan yang pertama di dunia dengan chuck hibrida HAIMER (HAIMER Hybrid Chuck). Ini menggabungkan sifat peredam getaran dari chuck hidrolik dengan chuck shrink fit berpresisi tinggi dan berkinerja tinggi, membuka banyak kemungkinan untuk membuat proses pemesinan menjadi lebih efisien dan berkelanjutan."