www.indo-industry.com
05
'12
Written on Modified on
Speedy delivery: Optimising parts management keeps production on schedule
Fischcon PV, the Dutch-based manufacturer of custom hydraulic packs and firefighting systems used in oil and gas exploration, found that creating a single, transparent process for managing the procurement of authorised components accelerated order fulfillment and provided numerous customer benefits.
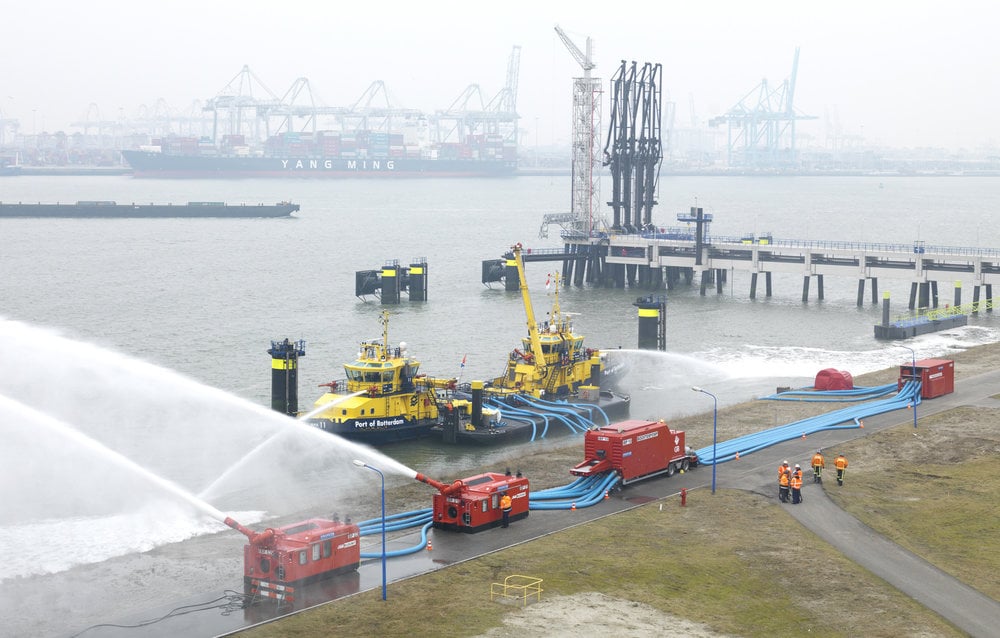
Ordering large components like motors or pumps often requires significant lead time. Manufacturing can’t begin until all components are on site. Any significant production delays expose the company to penalties. At the heart of the company’s streamlined procurement strategy is a centralised component database created two years ago in the mechanical PDM system used by its mechanical engineers. Fischcon’s electrical engineers work in EPLAN. Installing an interface made by EPLAN established a bidirectional EPLAN/PDM link so they could access the database. As a result, component management is accessible for all departments.
Linking EPLAN, ERP and PDM saves time and minimises errors
Using this integrated system to order the correct materials as early as possible, Fischcon began turning orders around more quickly, with much less risk of design or purchasing errors. “The connection between the ERP, PDM and EPLAN prevents miscommunication and unnecessary paper flows,” says engineering manager Pascal van der Jagt. “. We can see immediately whether all needed parts are on hand. Ordering the wrong one is almost impossible.” The database contains about 15,000 components. When fulfilling an order, a single bill of materials covering everything from the smallest bolt to the diesel engine or motor is compiled rather than separate ones for each engineering discipline. Working off a single BOM list helps purchasing recognise and troubleshoot delays before they become serious.
Active management pays off
The database is actively managed, which is well worth the cost, says van der Jagt. This ensures all component data is accurate, up to date and in standard format. Centralisation also made it possible to link component management to revision management. “As soon as a design revision is required, orders can be cancelled automatically and the appropriate substitutes ordered,” says van der Jagt. “The time savings in this respect are huge.”
Streamlining design of P&ID layouts in EPLAN PPE
Just over a year ago, the company began using EPLAN PPE to standardise and accelerate the creation of piping and instrumentation diagrams, which also meant faster customer approvals and component orders. We can shorten the turnaround time considerably says van der Jagt “Once the P&ID is approved by the client, it’s just a small step to realising a full equipment, instrument and piping list. We can order the main components more quickly.”
Standardised component management is a ´win-win`situation
Today, Fischcon can generate accurate project quotes sooner and provide customers with documents in a consistent format, whether it’s the P&ID, BOM, equipment, instrumentation and piping list, or the comprehensive documentation that goes with the completed job.
The benefits of centralised component management include significant financial savings for the company. For one of its larger systems, it has reduced time spent fulfilling orders by about 500 hours per unit, a 20% improvement that translates into annual savings of about €150,000.
Graphics
File: Spuitwagens.jpg
Caption: Firefighting system test at the port of Rotterdam
File: Spuitwagens:staand_beeld.jpg
Caption: Firefighting system test at the port of Rotterdam
File: Blauwe_box.jpg
Caption: 3D engineering design of a hydraulic power pack