www.indo-industry.com
26
'12
Written on Modified on
Faulhaber stepper motors regulate adaptive soldering and welding wire feed
Whether soldering, induction brazing or laser welding the weld filler metal is often delivered by wire. The system must always deliver a reproducible length of filler metal to the correct destination, but without jolting or bending the wire in the process. A new automatic wire feeder driven by a Faulhaber controlled micromotor is now providing a reliable solution to this problem.
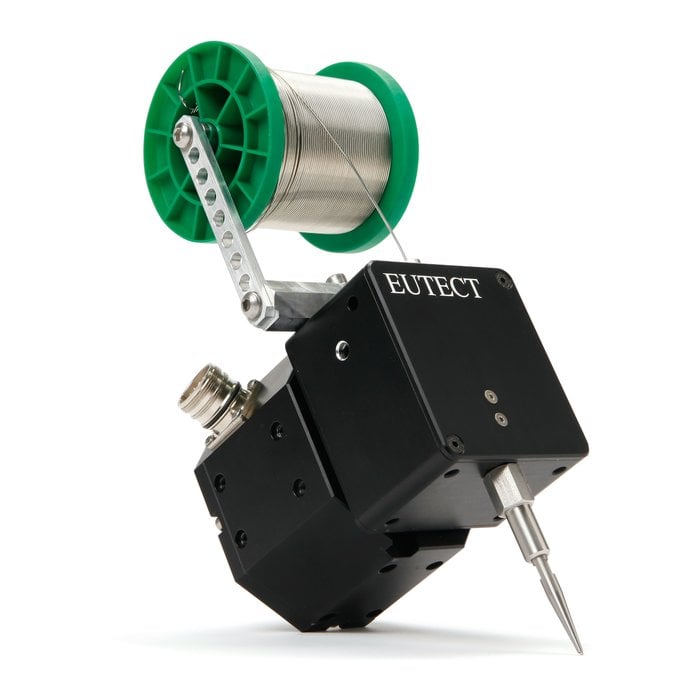
As the process principle is to deliver all filler metals to the workpiece in wire form, the new module has been designed to use a wide range of filler metals. Very different parameters such as wire thickness, wire stability and workpiece geometry have to be considered for the initial settings. This is why the wire feeder module incorporates various sensors that accurately identify the current wire position. This allows the system to deliver thin, soft soldering wire or relatively rigid steel wires for laser welding as required. The sophisticated sensor system teaches itself the joining process. However, without drives that accurately execute the control instructions, even the best data logging and evaluation system is to no effect. This is where compact microdrives come into play.
The wire is carried to the desired position via small stepper motors with a defined increment. The delivery rate results from the number of step pulses per unit time. In addition, an optical encoder signals the actual rotation to the controller. The encoder is positioned at the stepper motor drive wheel, where it detects slip and variations and thus measures the actual wire length being delivered. The large number of gear ratios offered by FAULHABER compact stepper motors means that the optimum gear ratio can be selected for each process requirement. The gear and stepper motor combination, designed to customer specification and currently offering gear ratios of between 14:1 and 134:1, allowed the developers to work with the action-reaction principle for the first time. In this case, an intelligent monitoring device measures the reaction force occurring when the wire contacts the soldering point. The high precision 22 mm stepper motors in combination with the encoder enable highly accurate control of the feed. The resulting wire feeding capabilities have already set new benchmarks for quality and reproducibility in various soldering and welding processes. The filler wire therefore functions like a virtually non-wearing mechanical sensing device directly at the site of the weld or solder. This also means that unavoidable variations in the positioning or geometry of the workpieces can be reliably identified concurrently with the joining process at that location.
The application calls for a simple motor with adjustable delivery rate and compression force. When comparing various drive systems in this respect, the two-phase stepper motor emerges as the best option. With 24 steps per revolution and a defined step width, it is easy to control. At the same time, it offers the option of a defined torque of almost 40 Nm if required. The compressive force of the weld filler material can therefore be maintained continuously in a wide range, while delivery rates can be easily varied, at a motor speed of more than 10,000 rpm or more than 4,000 steps per second. To guarantee the necessary precision, a plug-on optical encoder is additionally mounted to the drive control wheel. The encoders are capable of generating 100 to 500 pulses per revolution of the wheel shaft with or without zero reference pulse, or up to 1,024 pulses in high resolution. A reduction gear used in the application further improves the resolution at the drive roller that ultimately moves the welding wire.
Caption:
fau134_bild1.jpeg: Compact wire feed module for soldering and welding processes
fau134_bild5.jpeg: Compact drive module comprising stepper motor with plug-on encoder
fau134_bild4.jpeg: High-precision wire delivery despite compact size
dff11069.jpeg: Faulhaber controlled micromotor