www.indo-industry.com
11
'11
Written on Modified on
ROBA®-linearstop: A safety brake for dynamic linear-motion braking actions
Most of the brake elements available on the market today work purely as clamping units. They are only designed to secure the axes at a standstill, and are not suitable for dynamic braking procedures. The ROBA®-linearstop, however, is a fully adequate safety brake according to the Trade Association testing requirements. It enables reliable braking of axes in motion.
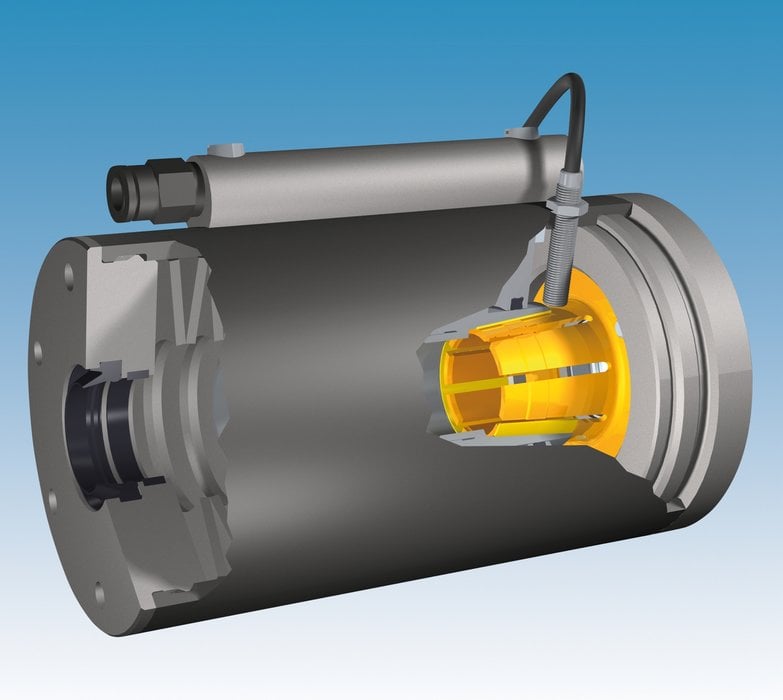
The dynamic safety brakes in the ROBA®-linearstop series work according to the fail-safe principle. The braking force is provided by pressure springs and transferred backlash-free via a conical surface onto a collet. This collet clamps the brake rod continuously, without changing its position. In closed position, the brake is able to withstand loads in both directions of motion. Dynamic braking actions can be achieved from speeds with a maximum of 2 m/s.
Dynamic stops were tested according to the Trade Association testing requirements on the mayr®-Drop Test Stand. In compliance with the Trade Association requirements, the tested elements are switched a million times statically and load-free, and a million times with load assumption. At every thousandth switching, they are braked dynamically from motion. The ROBA®-linearstop brake unit achieved 30,000 dynamic brake applications in fatigue tests with a maximum load and is therefore substantially better than the Trade Association testing requirement, which only stipulates 1,000 dynamic brake applications.
ROBA®-linearstop safety brakes can be mounted directly onto standard cylinders according to DIN ISO 15552. They can also be integrated simply, quickly and without complicated adjustment into different drive constellations. In contrast to other linear braking systems, the ROBA®-linearstop does not have to travel on the carriage. Supplying the pneumatic lines is therefore simplified. The brake can be screwed to a static machine component. The cylindrical piston rod is guided through the central bore of the brake and connected to the carriage of the linear drive.
As the carriage moves, this piston rod pushes itself axially through the ROBA®-linearstop. When the brake closes, the carriage is braked dynamically and then held backlash-free and accurately positioned. The axis is secured in both directions of motion. The brake is released pneumatically at 4 to 6 bar, according to the configured braking force. An integrated sensor continuously reports the switching status of the brake. The ROBA®-linearstop brake unit is supplied in four construction sizes with nominal retention forces of
1.5 kN up to 40 kN.
Product Fig.:
F-6-35-Bild1.jpg
Safety brakes of the ROBA®-linearstop series are designed for dynamic braking applications and can be mounted directly onto standard cylinders according to DIN ISO 15552.
Dynamic stops were tested according to the Trade Association testing requirements on the mayr®-Drop Test Stand. In compliance with the Trade Association requirements, the tested elements are switched a million times statically and load-free, and a million times with load assumption. At every thousandth switching, they are braked dynamically from motion. The ROBA®-linearstop brake unit achieved 30,000 dynamic brake applications in fatigue tests with a maximum load and is therefore substantially better than the Trade Association testing requirement, which only stipulates 1,000 dynamic brake applications.
ROBA®-linearstop safety brakes can be mounted directly onto standard cylinders according to DIN ISO 15552. They can also be integrated simply, quickly and without complicated adjustment into different drive constellations. In contrast to other linear braking systems, the ROBA®-linearstop does not have to travel on the carriage. Supplying the pneumatic lines is therefore simplified. The brake can be screwed to a static machine component. The cylindrical piston rod is guided through the central bore of the brake and connected to the carriage of the linear drive.
As the carriage moves, this piston rod pushes itself axially through the ROBA®-linearstop. When the brake closes, the carriage is braked dynamically and then held backlash-free and accurately positioned. The axis is secured in both directions of motion. The brake is released pneumatically at 4 to 6 bar, according to the configured braking force. An integrated sensor continuously reports the switching status of the brake. The ROBA®-linearstop brake unit is supplied in four construction sizes with nominal retention forces of
1.5 kN up to 40 kN.
Product Fig.:
F-6-35-Bild1.jpg
Safety brakes of the ROBA®-linearstop series are designed for dynamic braking applications and can be mounted directly onto standard cylinders according to DIN ISO 15552.