www.indo-industry.com
31
'10
Written on Modified on
Industrial refrigeration: Leroy-Somer meets the challenge
Leroy-Somer offers motor solutions to the users, installers and manufacturers of refrigeration equipment which are high-performance, compact and highly efficient: fixed-speed induction motors, high-efficiency motors, variable speed and, for peak productivity, the new Dyneo® permanent magnet solutions. This patented technology gives very high efficiency over the entire speed range, coupled with exceptional compactness, giving higher COP than with traditional solutions. This performance was demonstrated when J&E Hall International chose Leroy-Somer to drive its compressors. This major manufacturer of refrigeration equipment has just installed the refrigeration system for a new distribution centre belonging to Wm Morrison Supermarkets Plc. The energy savings have been estimated at about 45,000 euros over 4 years.
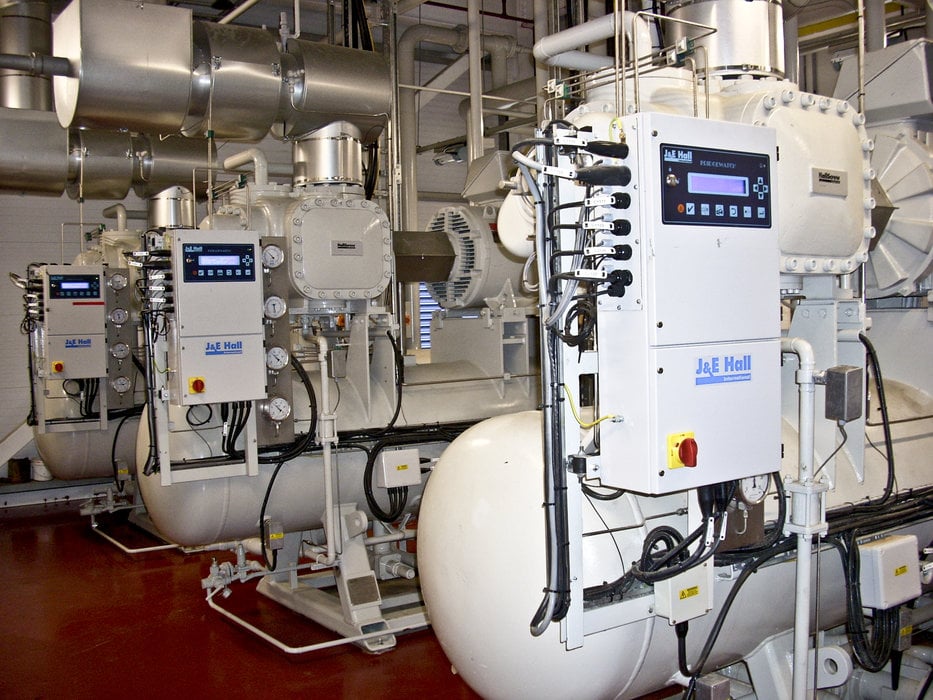
The challenge of saving energy
An industrial refrigeration installation is very energy-intensive and usually involves power ratings from 3 to 10 MW. In this context, electric motors are the focus of particular attention because they represent the main source of potential energy savings. For both installers and manufacturers, it is vital to promote technical solutions which improve the efficiency of installations.
The use of variable speed is certainly the first response to this challenge. The size of an installation depends on outdoor temperatures, primarily during the hottest periods. Outside of these periods, the installation is oversized. Variable speed can mitigate variations in thermal load, adapt machine operation to actual needs and therefore optimise the installation’s overall efficiency.
The Coefficient of Performance (COP) can prove an excellent tool to measure the efficiency of an installation. It expresses the ratio between the refrigerating capacity produced and the electrical power consumption. The higher this ratio, the more efficient the system is.
A complete, customised offer
With its broad experience in the design and manufacture of industrial drive systems, Leroy-Somer have developed an extensive range of solutions bringing significant energy savings.
Across its fixed-speed range, Leroy-Somer offer protected IP55 and -proof induction motors to meet IE2 classification as defined by the ErP European Directive (Energy related Product, formerly EuP). This range includes some series which already conform to the IE3 “Premium” efficiency class.
For variable speed, Leroy-Somer offers the widest range in the market, from a simple speed control to a full specification system through a decentralised variable speed control, Several special series of motors have been designed to provide a solid response to the needs of different applications, and to ensure the highest possible performance of an electronic drive system: high efficiency, constant torque operation without de-rating or forced ventilation to reduce maintenance and breakdown risks...
The company has also been developing new drive technologies particularly well-suited to this market: the Dyneo® range combines solutions including Leroy Somer drives and synchronous permanent magnet motors. The patented radial magnet rotor technology, by eradicating energy losses due to the rotor parts, has led to significant increases in machine efficiency, particularly when operating under highly variable load. These unrivalled efficiency levels are already far above the minimum thresholds for the forthcoming IE4 class, heralding additional energy savings of more than 10% compared to traditional variable speed solutions. The return on investment for these new technologies is therefore very often less than 12 months.
This innovative technology, tried and tested for more than 10 years by leading compressor manufacturers, has the advantage of being exceptionally compact, giving higher COP than with traditional solutions, whilst reducing maintenance costs.
For the refurbishment of existing systems, the LSRPM series, whose mechanical construction is identical to that of an induction motor, proves extremely easy to use. In addition to contributing significant energy savings, the return on investment is extremely rapid.
Finally, in its role as an international group, the company offers assistance to installers throughout the world, whether in setting up new plants or maintaining existing plants.
Spotlight on the efficient new DYNEO® solution from Leroy-Somer: Wm Morrison Supermarkets Plc
With the creation of their newest distribution centre in the UK, Wm Morrison Supermarkets Plc continue with their goal "Fresh food for you", placing environmental concerns at the heart of their design process.
J&E Hall International, a major supplier of refrigeration equipment, were able with their compressor pack to meet the energy challenge facing Wm Morrison Supermarkets Plc.
J&E Hall's approach is to combine both the fixed speed refrigeration pack with the variable speed refrigeration pack used to regulate the system depending on the demand.
In order to maximise energy savings, J&E Hall worked on two solutions for the variable speed pack: one using existing asynchronous induction motor technology and the other one using the new Leroy Somer innovation Dyneo. After in-depth analysis, the compressor developer decided to use the new Dyneo concept.
The graph below shows the difference between the efficiency of the Dyneo permanent magnet (PM) motor and the Eff2 asynchronous induction motor.
Over a speed range of 3600 rpm down to 1000 rpm, the difference in the efficiency level between the motors can be up to 7.5 percent.
The plant is running 7 days a week, 365 days a year.
The following illustration shows the energy saving achieved with Dyneo depending on the customer’s duty cycle:
Eff2 motor = consumption of 2,899,243 kWh, i.e. a cost of £231,937 (€274,088)
Dyneo = consumption of 2,780,802 kWh, i.e. a cost of £222,464 (€262,893).
The annual saving is therefore £9,473 (€11,194). The total energy consumption of the standard motor includes the 3 kW forced ventilation. The calculation is based on a cost of 8p per kW. Energy saved after 4 years = £37,892 (€44,776).
Duncan ASPINALL, J&E Hall's project manager, explains: ‘Our customers are more and more concerned by their energy bill and without doubt, Dyneo® is the right solution. This motor will have a bright future, fitted on J&E Hall's screw compressors.’
An industrial refrigeration installation is very energy-intensive and usually involves power ratings from 3 to 10 MW. In this context, electric motors are the focus of particular attention because they represent the main source of potential energy savings. For both installers and manufacturers, it is vital to promote technical solutions which improve the efficiency of installations.
The use of variable speed is certainly the first response to this challenge. The size of an installation depends on outdoor temperatures, primarily during the hottest periods. Outside of these periods, the installation is oversized. Variable speed can mitigate variations in thermal load, adapt machine operation to actual needs and therefore optimise the installation’s overall efficiency.
The Coefficient of Performance (COP) can prove an excellent tool to measure the efficiency of an installation. It expresses the ratio between the refrigerating capacity produced and the electrical power consumption. The higher this ratio, the more efficient the system is.
A complete, customised offer
With its broad experience in the design and manufacture of industrial drive systems, Leroy-Somer have developed an extensive range of solutions bringing significant energy savings.
Across its fixed-speed range, Leroy-Somer offer protected IP55 and -proof induction motors to meet IE2 classification as defined by the ErP European Directive (Energy related Product, formerly EuP). This range includes some series which already conform to the IE3 “Premium” efficiency class.
For variable speed, Leroy-Somer offers the widest range in the market, from a simple speed control to a full specification system through a decentralised variable speed control, Several special series of motors have been designed to provide a solid response to the needs of different applications, and to ensure the highest possible performance of an electronic drive system: high efficiency, constant torque operation without de-rating or forced ventilation to reduce maintenance and breakdown risks...
The company has also been developing new drive technologies particularly well-suited to this market: the Dyneo® range combines solutions including Leroy Somer drives and synchronous permanent magnet motors. The patented radial magnet rotor technology, by eradicating energy losses due to the rotor parts, has led to significant increases in machine efficiency, particularly when operating under highly variable load. These unrivalled efficiency levels are already far above the minimum thresholds for the forthcoming IE4 class, heralding additional energy savings of more than 10% compared to traditional variable speed solutions. The return on investment for these new technologies is therefore very often less than 12 months.
This innovative technology, tried and tested for more than 10 years by leading compressor manufacturers, has the advantage of being exceptionally compact, giving higher COP than with traditional solutions, whilst reducing maintenance costs.
For the refurbishment of existing systems, the LSRPM series, whose mechanical construction is identical to that of an induction motor, proves extremely easy to use. In addition to contributing significant energy savings, the return on investment is extremely rapid.
Finally, in its role as an international group, the company offers assistance to installers throughout the world, whether in setting up new plants or maintaining existing plants.
Spotlight on the efficient new DYNEO® solution from Leroy-Somer: Wm Morrison Supermarkets Plc
With the creation of their newest distribution centre in the UK, Wm Morrison Supermarkets Plc continue with their goal "Fresh food for you", placing environmental concerns at the heart of their design process.
J&E Hall International, a major supplier of refrigeration equipment, were able with their compressor pack to meet the energy challenge facing Wm Morrison Supermarkets Plc.
J&E Hall's approach is to combine both the fixed speed refrigeration pack with the variable speed refrigeration pack used to regulate the system depending on the demand.
In order to maximise energy savings, J&E Hall worked on two solutions for the variable speed pack: one using existing asynchronous induction motor technology and the other one using the new Leroy Somer innovation Dyneo. After in-depth analysis, the compressor developer decided to use the new Dyneo concept.
The graph below shows the difference between the efficiency of the Dyneo permanent magnet (PM) motor and the Eff2 asynchronous induction motor.
Over a speed range of 3600 rpm down to 1000 rpm, the difference in the efficiency level between the motors can be up to 7.5 percent.
The plant is running 7 days a week, 365 days a year.
The following illustration shows the energy saving achieved with Dyneo depending on the customer’s duty cycle:
Eff2 motor = consumption of 2,899,243 kWh, i.e. a cost of £231,937 (€274,088)
Dyneo = consumption of 2,780,802 kWh, i.e. a cost of £222,464 (€262,893).
The annual saving is therefore £9,473 (€11,194). The total energy consumption of the standard motor includes the 3 kW forced ventilation. The calculation is based on a cost of 8p per kW. Energy saved after 4 years = £37,892 (€44,776).
Duncan ASPINALL, J&E Hall's project manager, explains: ‘Our customers are more and more concerned by their energy bill and without doubt, Dyneo® is the right solution. This motor will have a bright future, fitted on J&E Hall's screw compressors.’