www.indo-industry.com
23
'09
Written on Modified on
The End of Percussion Maintenance
Now operating on more than 300,000 pumps worldwide, the new Ingersoll Rand motor technology for diaphragm pumps is a true success story. The technology combats three confounding pump motor issues: freezing, stalling and poor energy efficiency. With the purchase price of diaphragm pumps comprising as little as 5% of the overall cost of ownership, the benefit of Ingersoll Rand’s innovative technology is clear. Operating for five years on all Expert series pumps (3/8’’ to 2’’ for non metal pumps, ½’’ to 3’’ for metal pumps), it has brought operating costs down by 20% to 50 %.
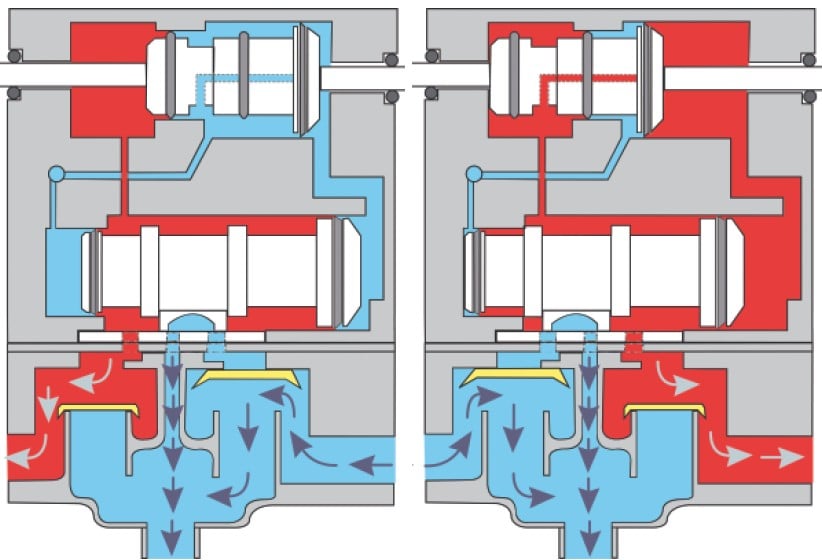
“Percussion maintenance”, a technique commonly used on failing pumps where a technician beats on the pump’s stalled motor with a hammer or rubber mallet, often indicates motor deficiencies in the diaphragm pump. Ingersoll Rand’s innovative pump design has eradicated the problem.
Problem: Freezing
Freezing is a chronic issue that causes a motor to seize up and fail in many applications. Freezing occurs as compressed air expands and creates a severe decrease in pressure. As the air returns to atmospheric pressure, it becomes extremely cold, freezing any moisture in the air supply. This cold air has been measured as low as -30 degrees, causing ice particles to accumulate and clog the motor area and muffler. The ice build-up stalls the pump, leaving it down until ambient air or another device can melt the ice. Many facilities develop workarounds, such as implementing space heaters, hot water taps and other thawing mechanisms. However, these efforts tie up the maintenance team and require additional resources.
Ingersoll Rand’s solution is a new pump design that exhausts air from the chamber as quickly as possible. Exhaust is prohibited from travelling through critical motor components, such as the spool valves. This design mainly relies on an innovative valve, the Quick DumpTM, which diverts cold- and wet-exhaust air away from the major air valve.
Problem: Stalling
Conventional valves feature a “balanced” design in which the valve is too evenly weighted. Air valves using this design often generate poor shift signals and, over time, the valve centers with an equal pressure differential on both sides. These pressures cancel each other out and the air valve does not shift, causing the pump to stall. Ingersoll Rand teams have design a new “unbalanced” valve that eliminates air valve centering. This air valve design features a large diameter on one end of the valve and a small diameter on the opposite end, creating an optimal pressure differential. Since the valves are always biased toward one side, they do not center out and stall the pump, even under low air inlet pressures.
Problem: Poor Energy Efficiency
Many manufacturers utilize an O-ring configuration on spools to prevent air leakage, but this design often wears and creates a poor seal, creating air blow-by and reducing efficiency. Blow-by is also caused by a metal-to-metal lapped-fit valve design. This model utilizes a spool with a slightly smaller diameter than the bore it sits in, creating a gap that allows compressed air to escape.
The Ingersoll solution, named the “D-Valve” consists of a positive seal on the valve spool created by U-cups to maximize energy efficiency. These prevent air leakage by providing a positive seal as the valve shifts. Additionally, seal points are made of solid materials where applicable (ceramic components are often best) to ensure longer life. Special materials, such as over-molded sleeves, are utilized to increase lubricity and reduce or eliminate wear in the valving mechanisms.
Captions:
Valve Cut-away.jpeg: Ingersoll Rand innovative diaphragm pump design
QuickDump.jpeg: Quick Dump valves eliminate freezing
Exp_Pump_Group.jpeg: The Exp range, equipped with innovative air motor technology
Contact: Karina Visciola
Email: This email address is being protected from spambots. You need JavaScript enabled to view it.
Website: www.fluids.ingersollrand.com
Problem: Freezing
Freezing is a chronic issue that causes a motor to seize up and fail in many applications. Freezing occurs as compressed air expands and creates a severe decrease in pressure. As the air returns to atmospheric pressure, it becomes extremely cold, freezing any moisture in the air supply. This cold air has been measured as low as -30 degrees, causing ice particles to accumulate and clog the motor area and muffler. The ice build-up stalls the pump, leaving it down until ambient air or another device can melt the ice. Many facilities develop workarounds, such as implementing space heaters, hot water taps and other thawing mechanisms. However, these efforts tie up the maintenance team and require additional resources.
Ingersoll Rand’s solution is a new pump design that exhausts air from the chamber as quickly as possible. Exhaust is prohibited from travelling through critical motor components, such as the spool valves. This design mainly relies on an innovative valve, the Quick DumpTM, which diverts cold- and wet-exhaust air away from the major air valve.
Problem: Stalling
Conventional valves feature a “balanced” design in which the valve is too evenly weighted. Air valves using this design often generate poor shift signals and, over time, the valve centers with an equal pressure differential on both sides. These pressures cancel each other out and the air valve does not shift, causing the pump to stall. Ingersoll Rand teams have design a new “unbalanced” valve that eliminates air valve centering. This air valve design features a large diameter on one end of the valve and a small diameter on the opposite end, creating an optimal pressure differential. Since the valves are always biased toward one side, they do not center out and stall the pump, even under low air inlet pressures.
Problem: Poor Energy Efficiency
Many manufacturers utilize an O-ring configuration on spools to prevent air leakage, but this design often wears and creates a poor seal, creating air blow-by and reducing efficiency. Blow-by is also caused by a metal-to-metal lapped-fit valve design. This model utilizes a spool with a slightly smaller diameter than the bore it sits in, creating a gap that allows compressed air to escape.
The Ingersoll solution, named the “D-Valve” consists of a positive seal on the valve spool created by U-cups to maximize energy efficiency. These prevent air leakage by providing a positive seal as the valve shifts. Additionally, seal points are made of solid materials where applicable (ceramic components are often best) to ensure longer life. Special materials, such as over-molded sleeves, are utilized to increase lubricity and reduce or eliminate wear in the valving mechanisms.
Captions:
Valve Cut-away.jpeg: Ingersoll Rand innovative diaphragm pump design
QuickDump.jpeg: Quick Dump valves eliminate freezing
Exp_Pump_Group.jpeg: The Exp range, equipped with innovative air motor technology
Contact: Karina Visciola
Email: This email address is being protected from spambots. You need JavaScript enabled to view it.
Website: www.fluids.ingersollrand.com