www.indo-industry.com
12
'09
Written on Modified on
The need for high density and modular connectors in the aeronautics market
In order to reduce the weight and to optimise information processing, the architecture of onboard electronic calculators has evolved from control units dedicated to a single function (integration of sensor signals, data fusion, image processing, etc.), to a multifunctional control unit. Connectors had to be adapted.
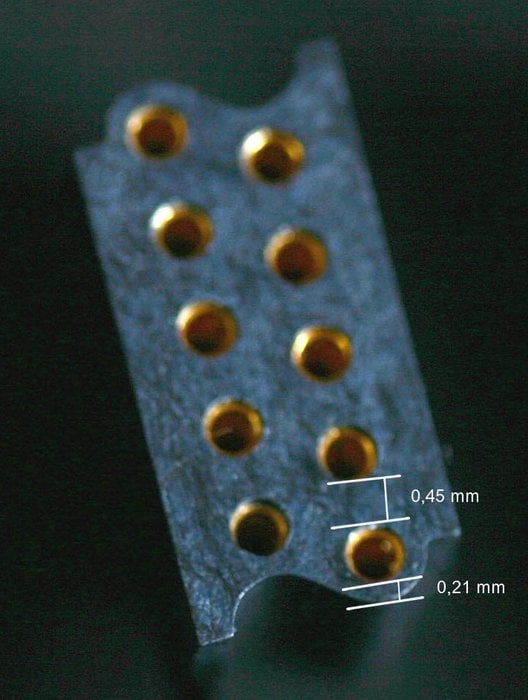
Reducing aircraft weight is essential to boost an aircraft’s fuel efficiency. It is very important in terms of costs but also to face the ever-increasing distances that airplanes of the future are expected to travel. But, exploiting new materials is not the only way to do it. Reducing the number of components by simplifying the structure and composition of aircrafts electronic systems is also a very effective approach. This is not the only advantage. Simpler and more unified structures lend themselves to an easier assembling process and maintenance operations.
One of the big tendencies is to reduce the number of control units. This required the designing of processing units able to execute a range of up to four tasks in real time. There was thus a need to handle mixed signals and send them from one electronic board to another: digital, analogue, power, high frequency, Ethernet, etc., with an inexorable trend towards increasing bandwidth (up to 10 Gbits/s). Fiber optic connections are also more and more appreciated for their light weight and their high data rate. This in turn involved various types of connection (multiple connectors, extra wiring, etc.), thus increasing the risks of failure and adding to the complexity of installation and involving extra weight. Being able to develop a new connector to handle this signal became a critical issue.
The connector must achieve the feature of bringing most of these connections together in a single connector, in a very compact unit. Because it would be too costly to customise a connector for each individual need, the structure of this connector must be modular. This very high density connector would be made up of modules that can be freely assembled. The modules can be fitted with traditional electric signal contacts, coaxial, optical fibre or power contacts as design considerations require. It involves rethinking the classic mechanical limits for the sets of insulating connector contacts. The principle of stackable modules halves the thickness of the side walls between the exterior contact sockets (see Picture 1): from 0,45 mm to 0,21 mm.
To do this, Amphenol-Socapex has developed a new connector, named HILINX. It uses a specific S-shaped layout that enables the modules to be fitted together without losing contacts from one module to another (continuity of the spacing between contacts). The units are held in place by two stainless steel shells, one on each side.
This constraint imposed the necessity of making a plastic insulating block with very thin walls, which was nonetheless able to stand up to military and aeronautical environments (vibrations, thermal shocks, etc.). The parts must be free of all the defects commonly met with in plastics: no injection flashes, and no incomplete die fillings, to provide mechanical strength and protection from electric arcs (dielectric strength of 750 VRms at 60 Hz, in compliance with standard MIL-DTL-55302).
The manufacturing tolerances also had to be very small. To avoid all risks of pollution, the components have to be inserted without any lubricant. As such, the contacts are made to the required diameter without re-machining, to within a tolerance of 0.03 mm for certain sizes.
New special tooling has been designed with minimal mechanical tolerances. The heat cycle is optimised in a closed loop to provide excellent die filling levels with very high dimensional precision (for injected plastics) and an excellent surface state. Plastic inserts provide dimensional tolerance levels of about 0.05 mm. The shells holding the modules together and providing contact continuity are made with tolerance levels of 0.03 mm. The clip and stud fixing system ensures perfect module positioning. A long programme of adjustment optimization was necessary to obtain these results. The manufacturing process is checked by taking test samples.
The shells are bonded to the preassembled modules using a dual component structural adhesive that stands up well to thermal expansion and moisture, and complies with aeronautical requirements.
The insulating material used is an LCP (Liquid Crystal Polymer) thermoplastic. It provides enhanced electrical characteristics, better resistance to heat and chemical attacks, excellent dimensional stability, and good characteristics for plastic injection. Furthermore, it stands up to flame tests. The moisture regain levels are also very low.
The stacked construction without loss of contacts ensures perfect continuity in the contact alignments. This means that the connector thus obtained is 100% compatible (in the signal contact version only) with well-known aeronautical standard one-piece connectors (M55302/190 to /193).
The pitch between signal contacts is 1.905 mm, in a staggered arrangement. The modules can be made up of 2, 3, 4 or 6 rows. The signal contacts feature the Starclip principle, which provides unique reliability characteristics, tested in accordance with standard MIL DTL 55302, and stands up to more severe tests involving vibrations and shocks (monitoring of electrical continuity at 2 ns in dynamic mode during the tests).
Amphenol provides the widest range of contacts on the market: Copper (Signals, power, HF, Quadrax, etc.) and Optical Fibres (Butt joints, lenses, etc.). For example, hybrid interconnections can be fitted for RADSOK® power contacts. The 2.4 mm diameter male contacts can put through currents of up to 35A while taking up very little space in modules with 3 rows of signal contacts.
The connectors are designed for harsh environments: the admissible temperature range is -65°C to +150°C, and they stand up to salt spray for 96 hours. They also stand up to shocks and vibrations, in accordance with the normative tests SAE AS 13441, 2004 and 2005 methods, and also to other vibratory spectra that are specific to certain aeronautical programmes. The maximum electrical resistance of the signal contacts is 10 mohms.
The applications of this new kind of connector lie mainly in aeronautics, but they are also used in the medical, automatic controller, railway and oil exploration fields - and in military applications in general. HiLinx facilitates design work for printed circuit connections and reduces the number of components, while featuring maximum performance and reliability levels. It provides solutions that are often more compact and less expensive.
Picture 2, 3 and 4: Examples of mixed signals in the same connector.
One of the big tendencies is to reduce the number of control units. This required the designing of processing units able to execute a range of up to four tasks in real time. There was thus a need to handle mixed signals and send them from one electronic board to another: digital, analogue, power, high frequency, Ethernet, etc., with an inexorable trend towards increasing bandwidth (up to 10 Gbits/s). Fiber optic connections are also more and more appreciated for their light weight and their high data rate. This in turn involved various types of connection (multiple connectors, extra wiring, etc.), thus increasing the risks of failure and adding to the complexity of installation and involving extra weight. Being able to develop a new connector to handle this signal became a critical issue.
The connector must achieve the feature of bringing most of these connections together in a single connector, in a very compact unit. Because it would be too costly to customise a connector for each individual need, the structure of this connector must be modular. This very high density connector would be made up of modules that can be freely assembled. The modules can be fitted with traditional electric signal contacts, coaxial, optical fibre or power contacts as design considerations require. It involves rethinking the classic mechanical limits for the sets of insulating connector contacts. The principle of stackable modules halves the thickness of the side walls between the exterior contact sockets (see Picture 1): from 0,45 mm to 0,21 mm.
To do this, Amphenol-Socapex has developed a new connector, named HILINX. It uses a specific S-shaped layout that enables the modules to be fitted together without losing contacts from one module to another (continuity of the spacing between contacts). The units are held in place by two stainless steel shells, one on each side.
This constraint imposed the necessity of making a plastic insulating block with very thin walls, which was nonetheless able to stand up to military and aeronautical environments (vibrations, thermal shocks, etc.). The parts must be free of all the defects commonly met with in plastics: no injection flashes, and no incomplete die fillings, to provide mechanical strength and protection from electric arcs (dielectric strength of 750 VRms at 60 Hz, in compliance with standard MIL-DTL-55302).
The manufacturing tolerances also had to be very small. To avoid all risks of pollution, the components have to be inserted without any lubricant. As such, the contacts are made to the required diameter without re-machining, to within a tolerance of 0.03 mm for certain sizes.
New special tooling has been designed with minimal mechanical tolerances. The heat cycle is optimised in a closed loop to provide excellent die filling levels with very high dimensional precision (for injected plastics) and an excellent surface state. Plastic inserts provide dimensional tolerance levels of about 0.05 mm. The shells holding the modules together and providing contact continuity are made with tolerance levels of 0.03 mm. The clip and stud fixing system ensures perfect module positioning. A long programme of adjustment optimization was necessary to obtain these results. The manufacturing process is checked by taking test samples.
The shells are bonded to the preassembled modules using a dual component structural adhesive that stands up well to thermal expansion and moisture, and complies with aeronautical requirements.
The insulating material used is an LCP (Liquid Crystal Polymer) thermoplastic. It provides enhanced electrical characteristics, better resistance to heat and chemical attacks, excellent dimensional stability, and good characteristics for plastic injection. Furthermore, it stands up to flame tests. The moisture regain levels are also very low.
The stacked construction without loss of contacts ensures perfect continuity in the contact alignments. This means that the connector thus obtained is 100% compatible (in the signal contact version only) with well-known aeronautical standard one-piece connectors (M55302/190 to /193).
The pitch between signal contacts is 1.905 mm, in a staggered arrangement. The modules can be made up of 2, 3, 4 or 6 rows. The signal contacts feature the Starclip principle, which provides unique reliability characteristics, tested in accordance with standard MIL DTL 55302, and stands up to more severe tests involving vibrations and shocks (monitoring of electrical continuity at 2 ns in dynamic mode during the tests).
Amphenol provides the widest range of contacts on the market: Copper (Signals, power, HF, Quadrax, etc.) and Optical Fibres (Butt joints, lenses, etc.). For example, hybrid interconnections can be fitted for RADSOK® power contacts. The 2.4 mm diameter male contacts can put through currents of up to 35A while taking up very little space in modules with 3 rows of signal contacts.
The connectors are designed for harsh environments: the admissible temperature range is -65°C to +150°C, and they stand up to salt spray for 96 hours. They also stand up to shocks and vibrations, in accordance with the normative tests SAE AS 13441, 2004 and 2005 methods, and also to other vibratory spectra that are specific to certain aeronautical programmes. The maximum electrical resistance of the signal contacts is 10 mohms.
The applications of this new kind of connector lie mainly in aeronautics, but they are also used in the medical, automatic controller, railway and oil exploration fields - and in military applications in general. HiLinx facilitates design work for printed circuit connections and reduces the number of components, while featuring maximum performance and reliability levels. It provides solutions that are often more compact and less expensive.
Picture 2, 3 and 4: Examples of mixed signals in the same connector.