www.indo-industry.com
16
'08
Written on Modified on
The CRISTOPIA thermal energy storage system has been selected for the UFIDA Software Park.
With its 25 years of experience in thermal energy storage systems, the CIAT Group, is currently the world leader in the sector. In particular, the Company installed the first Ice storage system in China in 1992, for Electro Building Shenzhen. The new UFIDA Software Park contract is one more reference to be added to the 2,000 CRISTOPIA systems in operation worldwide, including Kempinski luftansa center in Beijing and the Hong Kong Asia World Expo. More than 5,000 MWh of electrical energy are saved every day thanks to CRISTOPIA equipment. Its range of use from -33°C to +27°C and its energy efficiency levels of 20% higher than those of the other solutions on the market are among the major factors contributing to its success.
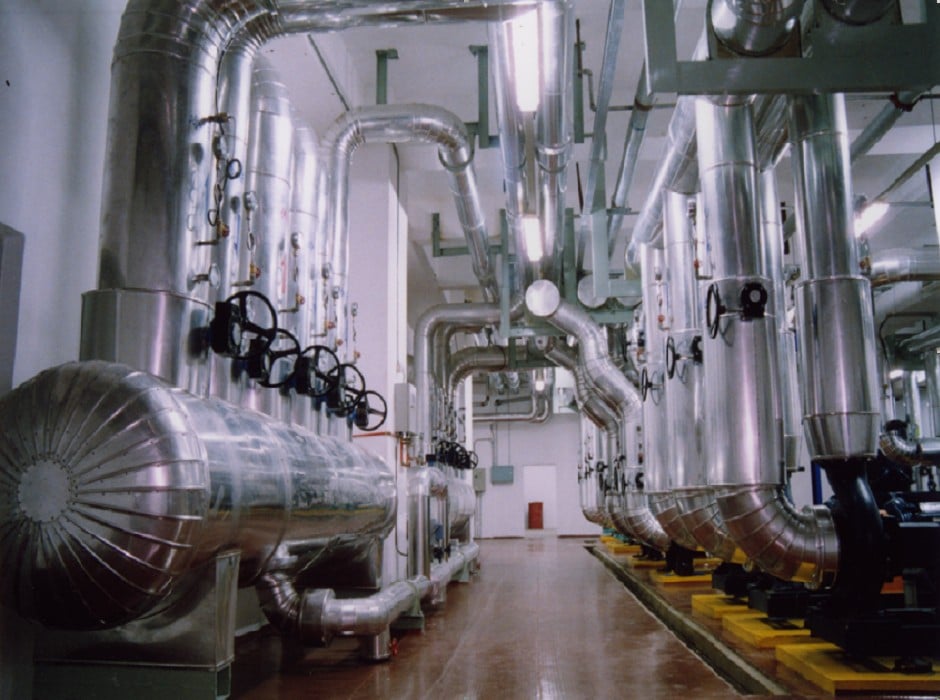
Thermal energy storage is a solution that is particularly well suited to services air conditioning and industrial refrigeration systems. Its operating principle consists of storing cold when electricity is cheap, available and outdoor temperatures are low, i.e. during the night, using a specially designed fluid, and giving it off during the day. By thus smoothing out refrigeration requirements, it enables reductions in energy consumption levels and in equipment sizing. Classical systems are designed for peak demand, even if we use the chillers at 100 % for only a few days or few hours every year. Thermal storage by latent heat allows a reduction in chiller capacity. This storage provides shortfall of the energy when demand is higher than the chiller capacity. Thus chiller operation is continuous and its efficiency at maximum.
The thermal energy storage system uses electrical power mainly at night, when thermal power stations operate at their highest levels of efficiency, thus reducing consumption of raw materials and helping to preserve the environment. The CRISTOPIA system regularly cuts the overall amounts of planned investments because it reduces the power ratings of the systems installed. In other cases, its average return on investment takes between 6 months and two years.
It has lots of advantages, starting with smaller sizing for the installation (from 30 to 70% for the chiller, cooling towers, electrical transformer, electrical cable, starting panel, substation etc ...). It also reduces electricity consumption by enhancing the energy efficiency of the refrigeration unit, and it enables use of electricity at the lowest rates. Lastly, it reduces the surface area of the technical installations, and in the event of a failure involving the main system, it can be used as a backup system. It is particularly well suited for services applications involving air conditioning (residential complexes, conference centres, supermarkets, offices, hospitals, etc.), refrigeration (pharmaceuticals and dairy industries, bottling plants, abattoirs, etc.) or backup systems (telephone exchanges, computer rooms, cold stores, etc.).
The CRISTOPIA system is based on nodules, polyolefin spheres that are obtained by extrusion blow moulding. The nodules are filled with phase change materials (solid-liquid). Contrary to systems using coils, which freeze water outside the coils, spherical nodules have a larger heat exchange surface area, so they absorb cold faster. The freezing temperature of the PCM is at -5 or -6°C, whereas in other solutions, it stands at -8° or -9°. CRISTOPIA thus provides energy savings of over 20% as compared with other solutions. CRISTOPIA products cover a range of melting temperatures from -33°C to +27 °C. To better meet the specific requirements of each application, CRISTOPIA provides a range of 12 different types of nodules, with varying levels of latent heat. To add to their remarkable thermal efficiency in terms of heat exchange power, CRISTOPIA nodules have an exceptionally long service life (the equivalent of 30 to 40 years and even more of use under normal conditions).
Operating principle:
Storage only: During the night, energy is stored using the refrigeration unit to cool the heat transfer fluid. The fluid circulates at temperatures below the melting temperature of the phase change material contained in the nodules, leading to its crystallization. Energy is thus stored using the latent heat of crystallization.
Direct production: While cooling requirements are below the power rating of the refrigeration unit, the refrigeration power required is provided directly by the unit on its own. The refrigeration unit regulates its power output.
Release only: The thermal energy storage system can be used on its own without calling on the refrigeration unit (in backup mode or during peak rate periods). The heat transfer fluid enters the system at a temperature above the melting point of the phase change materials and it is cooled through contact with the nodules. The outlet temperature is controlled by the 3-way valve according to demand.
Direct production + release: When demand outstrips the cooling power of the refrigeration unit, it is met by combined operation of the unit and the storage system.
Direct production + storage: In this operating mode (usually at night) the refrigeration unit cools the storage system and meets the night-time requirements (limited to 10 / 15% of the rated unit power for storage system cooling). The refrigeration unit is regulated via its outlet temperature.
The refrigeration storage tank is sized to suit the site and the system capacity. It can be cylindrical or parallelepiped (made of concrete or steel). Cylindrical tanks can be installed indoors, outdoors or below ground. The tank features an upper manhole that is used to fill it with nodules and a lower manhole to drain it if necessary. Two upper and lower diffusers are used to spread the heat transfer fluid throughout the tank for optimum efficiency. The heat exchange between the nodules and the system is carried out via a heat transfer fluid circulating inside the tank.
Ciat Group is also able to provide several types of services, starting with a test platform that has been set up to provide pertinent advice as to use of the refrigeration storage system (hydraulic diagram, control systems, the various possible strategies, etc.). The test platform can also be used to simulate a project. Next, in the case of an existing building, to size the system correctly, it is important to determine the actual cooling requirements. Ciat Group has developed a measuring case that can be used to take measurements on the site. Lastly, to optimize sizing, a professional software program called Stockaid 2007 has been developed; it runs on Windows XP. Stockaid 2007 uses the histogram of the cooling requirements and the temperature regime in the distribution circuit (outlet and return) to select the type of nodules and calculate the volume required, together with the reduced cooling power needed. The software enables our technical department to provide designers with the solutions that best suit their projects.
Ciat Group has developed an unique Control System “Cristo’Control2” for the management of the cooling plant.
Cristo'Control is a small electrical box (IP55) which must be supplied by UPS (protected against cut off) low tension power supply (24 VDC, 5A). It is ready to be connected to both general electric box electrical and measurement equipments. Cristo’Control does not supply the power and electrical protection of the installation equipment (valve running in 220V or pumps in 380V) but it manage the control of all the equipment thanks to dry contacts. The temperature probe, analogical signals (4-20mA, 0-10V) and other information thanks to dry contact will be connected directly to the Cristo’Control inlets.
Cristo'Control main functions are:
-Automatic management of authorized operating modes
According to the determined parameters (time, tariff sections, actual cooling demand, energy available, etc...) Cristo'Control allows the appropriate operating mode. In the case of equipment default, Cristo’Control chooses the best operating strategy waiting for the intervention of the servicing technician.
-Control of the cooling production network
Cristo'Control controls all the circulating units of primary cooling production including plate heat exchanger and chillers (on/off chiller, set point temperature, 3 ways valve regulation, openings/closings of valves...).
-Alarms and defaults report
Alarms and defaults message are sent to an entity in charge of the installation servicing (telephone, fax, email...).
-Remote follow-up in real time
Visualization of the installation, position of equipments and other operating parameters in real time by information report to the BMS (via RS485 link Modbus protocol in standard). It is also possible to obtain an access by a Web navigator through the Cristo'Control Web site (data are punctually refreshed)
-Collection of operating parameters and measured values
The access to the values and information collection enclosed in a history database allows to: asses periodical energy balances of the installation, analyse and optimise the operation of the cooling production according to the evolution of demand, analyse the reasons of parameter drifts and start the appropriate maintenance mode (preventive servicing).
Cristo'Control Web site
Ciat Group has created an Internet server fully dedicated to Cristo'Control. It provides all the application of Cristo’Control and a long-term saving of measurement (operating parameters). This web site gives an access to operating parameters, events and measurements in reading only (for security reasons). Each installation has its own private and protected connection. It also provides diagrams and table of processing data (thermal balance, curve, efficiency, statistics…). The access to this server and all its functionality (internet connexion with a web navigator as internet explorer for example) is a free service the first year after commissioning. Then it is subject to a annual subscription (offer available on request). The address of Cristo’Control’s web site is: www.cristocontrol.com
Monitoring the installation process
The monitoring of the installation can be done locally (display panel of the Cristo'Control box) and remotely (information sending with one /or several off-set stations). The remote control is done through connection series and/or a telephone line (by the servicing company or any other entity chosen by the owner of the installation).
Installation’s follow-up
The owner, or the entity chosen, must be informed in real time of the evolution of the parameters to ensure and to preserve optimal performances. Also the measurement drifts relative to the right operation, allows forestalling a possible problem and starting a preventive maintenance process. A control dashboard is available on the www.cristocontrol.com which presents all the necessary parameters for the continuous observation of drifts.
The thermal energy storage system uses electrical power mainly at night, when thermal power stations operate at their highest levels of efficiency, thus reducing consumption of raw materials and helping to preserve the environment. The CRISTOPIA system regularly cuts the overall amounts of planned investments because it reduces the power ratings of the systems installed. In other cases, its average return on investment takes between 6 months and two years.
It has lots of advantages, starting with smaller sizing for the installation (from 30 to 70% for the chiller, cooling towers, electrical transformer, electrical cable, starting panel, substation etc ...). It also reduces electricity consumption by enhancing the energy efficiency of the refrigeration unit, and it enables use of electricity at the lowest rates. Lastly, it reduces the surface area of the technical installations, and in the event of a failure involving the main system, it can be used as a backup system. It is particularly well suited for services applications involving air conditioning (residential complexes, conference centres, supermarkets, offices, hospitals, etc.), refrigeration (pharmaceuticals and dairy industries, bottling plants, abattoirs, etc.) or backup systems (telephone exchanges, computer rooms, cold stores, etc.).
The CRISTOPIA system is based on nodules, polyolefin spheres that are obtained by extrusion blow moulding. The nodules are filled with phase change materials (solid-liquid). Contrary to systems using coils, which freeze water outside the coils, spherical nodules have a larger heat exchange surface area, so they absorb cold faster. The freezing temperature of the PCM is at -5 or -6°C, whereas in other solutions, it stands at -8° or -9°. CRISTOPIA thus provides energy savings of over 20% as compared with other solutions. CRISTOPIA products cover a range of melting temperatures from -33°C to +27 °C. To better meet the specific requirements of each application, CRISTOPIA provides a range of 12 different types of nodules, with varying levels of latent heat. To add to their remarkable thermal efficiency in terms of heat exchange power, CRISTOPIA nodules have an exceptionally long service life (the equivalent of 30 to 40 years and even more of use under normal conditions).
Operating principle:
Storage only: During the night, energy is stored using the refrigeration unit to cool the heat transfer fluid. The fluid circulates at temperatures below the melting temperature of the phase change material contained in the nodules, leading to its crystallization. Energy is thus stored using the latent heat of crystallization.
Direct production: While cooling requirements are below the power rating of the refrigeration unit, the refrigeration power required is provided directly by the unit on its own. The refrigeration unit regulates its power output.
Release only: The thermal energy storage system can be used on its own without calling on the refrigeration unit (in backup mode or during peak rate periods). The heat transfer fluid enters the system at a temperature above the melting point of the phase change materials and it is cooled through contact with the nodules. The outlet temperature is controlled by the 3-way valve according to demand.
Direct production + release: When demand outstrips the cooling power of the refrigeration unit, it is met by combined operation of the unit and the storage system.
Direct production + storage: In this operating mode (usually at night) the refrigeration unit cools the storage system and meets the night-time requirements (limited to 10 / 15% of the rated unit power for storage system cooling). The refrigeration unit is regulated via its outlet temperature.
The refrigeration storage tank is sized to suit the site and the system capacity. It can be cylindrical or parallelepiped (made of concrete or steel). Cylindrical tanks can be installed indoors, outdoors or below ground. The tank features an upper manhole that is used to fill it with nodules and a lower manhole to drain it if necessary. Two upper and lower diffusers are used to spread the heat transfer fluid throughout the tank for optimum efficiency. The heat exchange between the nodules and the system is carried out via a heat transfer fluid circulating inside the tank.
Ciat Group is also able to provide several types of services, starting with a test platform that has been set up to provide pertinent advice as to use of the refrigeration storage system (hydraulic diagram, control systems, the various possible strategies, etc.). The test platform can also be used to simulate a project. Next, in the case of an existing building, to size the system correctly, it is important to determine the actual cooling requirements. Ciat Group has developed a measuring case that can be used to take measurements on the site. Lastly, to optimize sizing, a professional software program called Stockaid 2007 has been developed; it runs on Windows XP. Stockaid 2007 uses the histogram of the cooling requirements and the temperature regime in the distribution circuit (outlet and return) to select the type of nodules and calculate the volume required, together with the reduced cooling power needed. The software enables our technical department to provide designers with the solutions that best suit their projects.
Ciat Group has developed an unique Control System “Cristo’Control2” for the management of the cooling plant.
Cristo'Control is a small electrical box (IP55) which must be supplied by UPS (protected against cut off) low tension power supply (24 VDC, 5A). It is ready to be connected to both general electric box electrical and measurement equipments. Cristo’Control does not supply the power and electrical protection of the installation equipment (valve running in 220V or pumps in 380V) but it manage the control of all the equipment thanks to dry contacts. The temperature probe, analogical signals (4-20mA, 0-10V) and other information thanks to dry contact will be connected directly to the Cristo’Control inlets.
Cristo'Control main functions are:
-Automatic management of authorized operating modes
According to the determined parameters (time, tariff sections, actual cooling demand, energy available, etc...) Cristo'Control allows the appropriate operating mode. In the case of equipment default, Cristo’Control chooses the best operating strategy waiting for the intervention of the servicing technician.
-Control of the cooling production network
Cristo'Control controls all the circulating units of primary cooling production including plate heat exchanger and chillers (on/off chiller, set point temperature, 3 ways valve regulation, openings/closings of valves...).
-Alarms and defaults report
Alarms and defaults message are sent to an entity in charge of the installation servicing (telephone, fax, email...).
-Remote follow-up in real time
Visualization of the installation, position of equipments and other operating parameters in real time by information report to the BMS (via RS485 link Modbus protocol in standard). It is also possible to obtain an access by a Web navigator through the Cristo'Control Web site (data are punctually refreshed)
-Collection of operating parameters and measured values
The access to the values and information collection enclosed in a history database allows to: asses periodical energy balances of the installation, analyse and optimise the operation of the cooling production according to the evolution of demand, analyse the reasons of parameter drifts and start the appropriate maintenance mode (preventive servicing).
Cristo'Control Web site
Ciat Group has created an Internet server fully dedicated to Cristo'Control. It provides all the application of Cristo’Control and a long-term saving of measurement (operating parameters). This web site gives an access to operating parameters, events and measurements in reading only (for security reasons). Each installation has its own private and protected connection. It also provides diagrams and table of processing data (thermal balance, curve, efficiency, statistics…). The access to this server and all its functionality (internet connexion with a web navigator as internet explorer for example) is a free service the first year after commissioning. Then it is subject to a annual subscription (offer available on request). The address of Cristo’Control’s web site is: www.cristocontrol.com
Monitoring the installation process
The monitoring of the installation can be done locally (display panel of the Cristo'Control box) and remotely (information sending with one /or several off-set stations). The remote control is done through connection series and/or a telephone line (by the servicing company or any other entity chosen by the owner of the installation).
Installation’s follow-up
The owner, or the entity chosen, must be informed in real time of the evolution of the parameters to ensure and to preserve optimal performances. Also the measurement drifts relative to the right operation, allows forestalling a possible problem and starting a preventive maintenance process. A control dashboard is available on the www.cristocontrol.com which presents all the necessary parameters for the continuous observation of drifts.